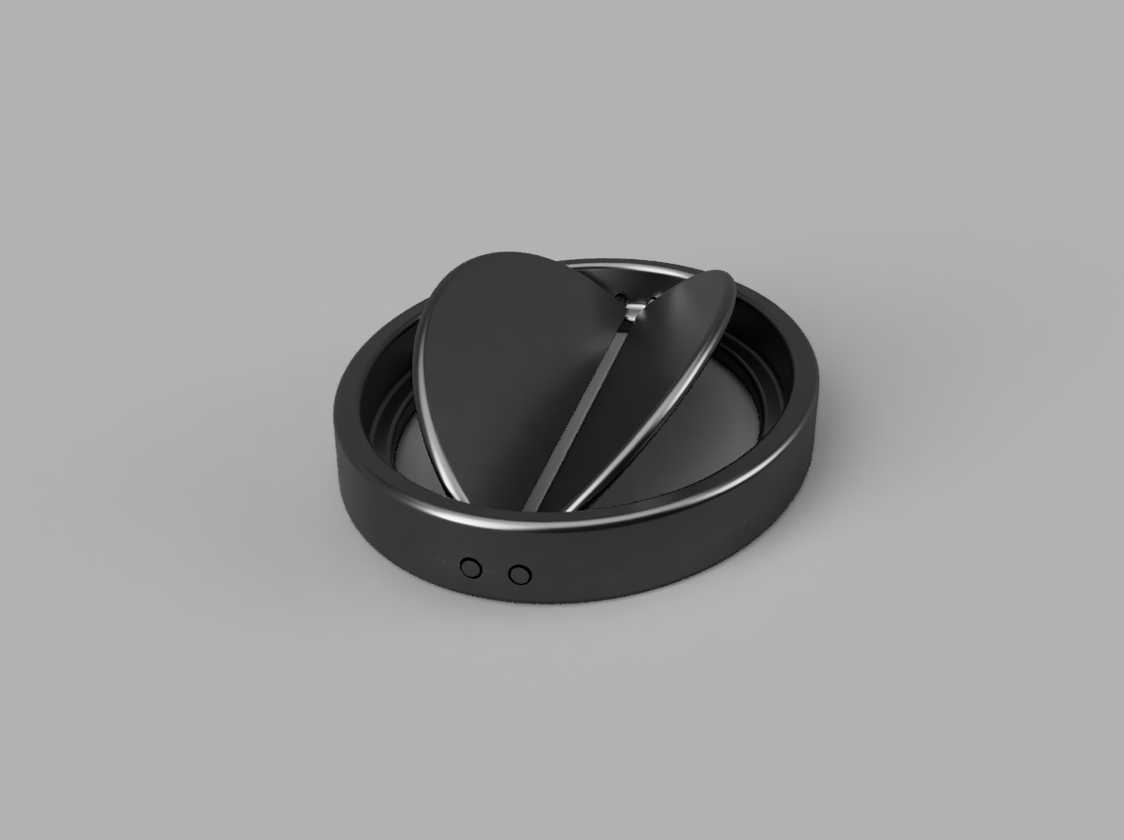
Isometric view of the top of a CAD model of the valve's final design iteration, with the leaflets shown in the open position
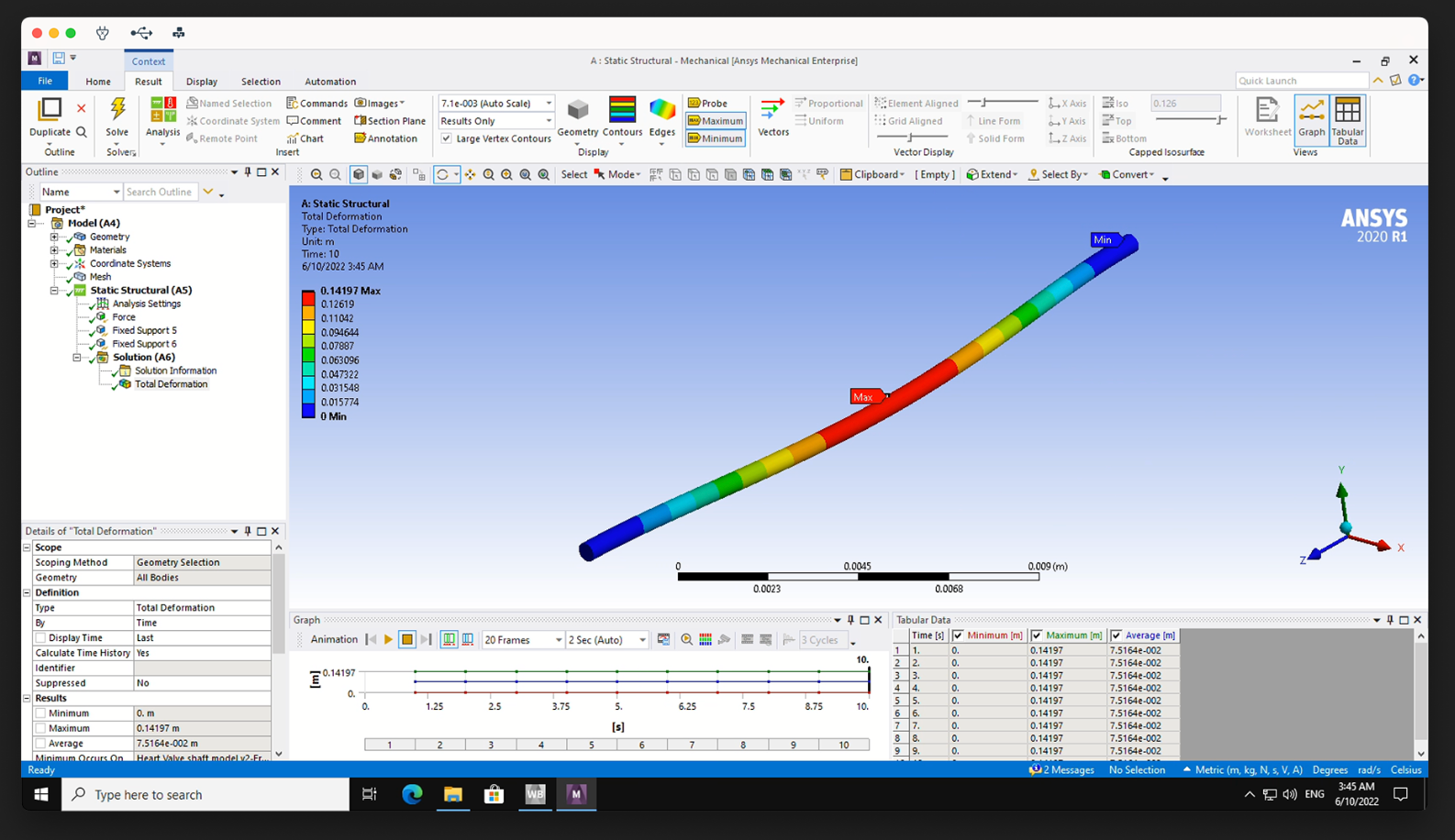
Screenshot of ANSYS Mechanical graphical user interface, showing a solution to a Static Structural deformation test on a shaft with the same dimensions as in the theoretical force analysis
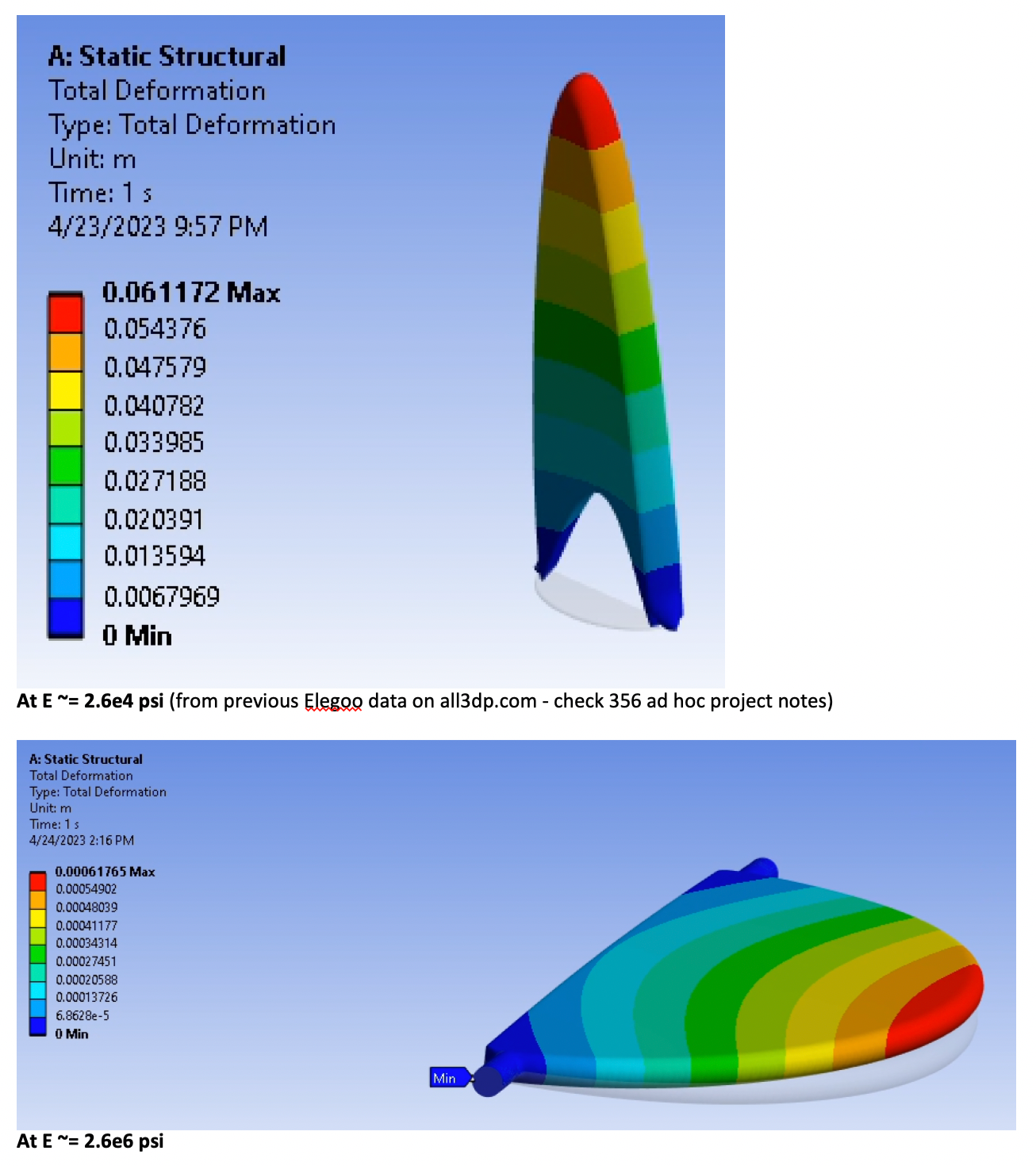
Screenshot of OneNote page showing static nonlinear deformation analysis results before (top) and after (bottom) 1e2 increase in E
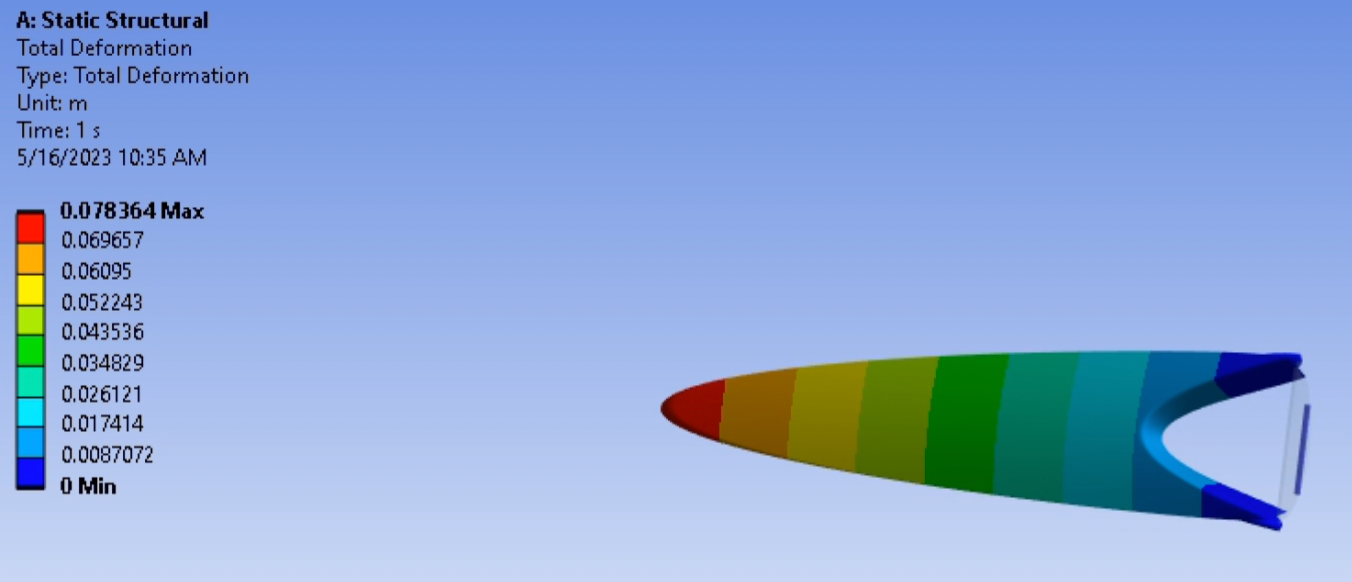
Static nonlinear analysis of resin leaflet colliding with block upon downward application of force. Something is clearly wrong here, as material changes fixed it...
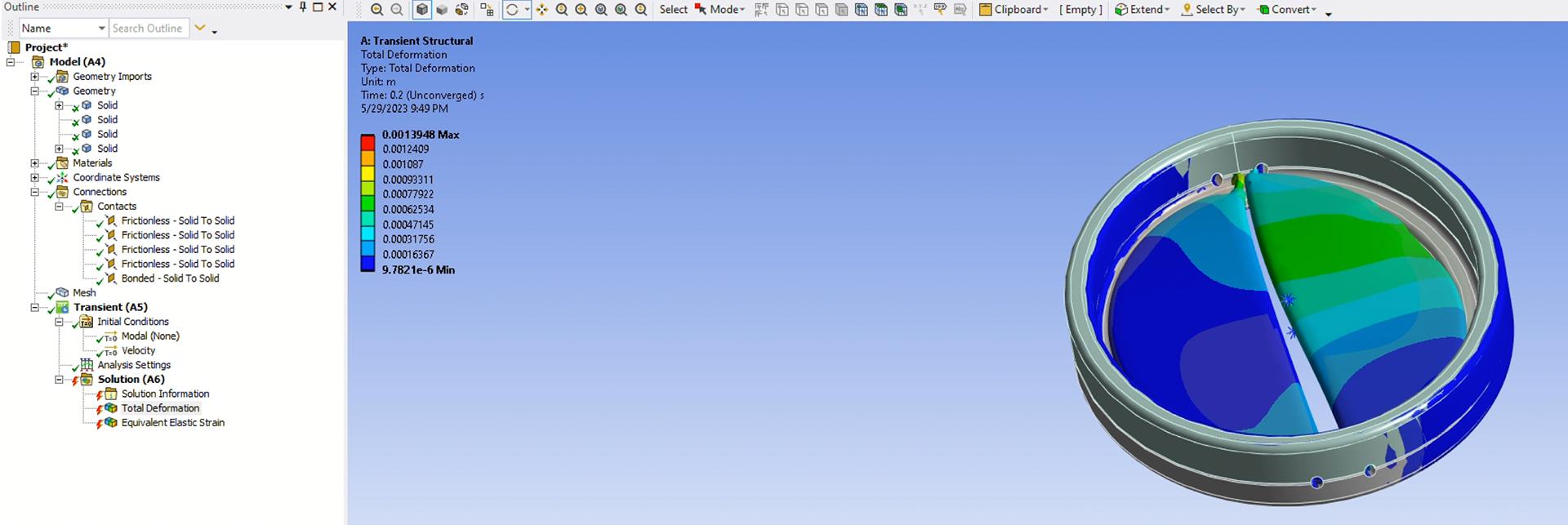
Incomplete results and the objects used to generate them
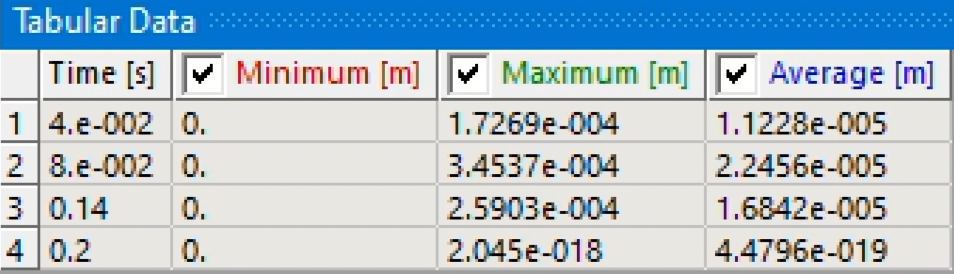
Minimum, maximum, and average leaflet deformation values on the leaflet using Transient Structural analysis
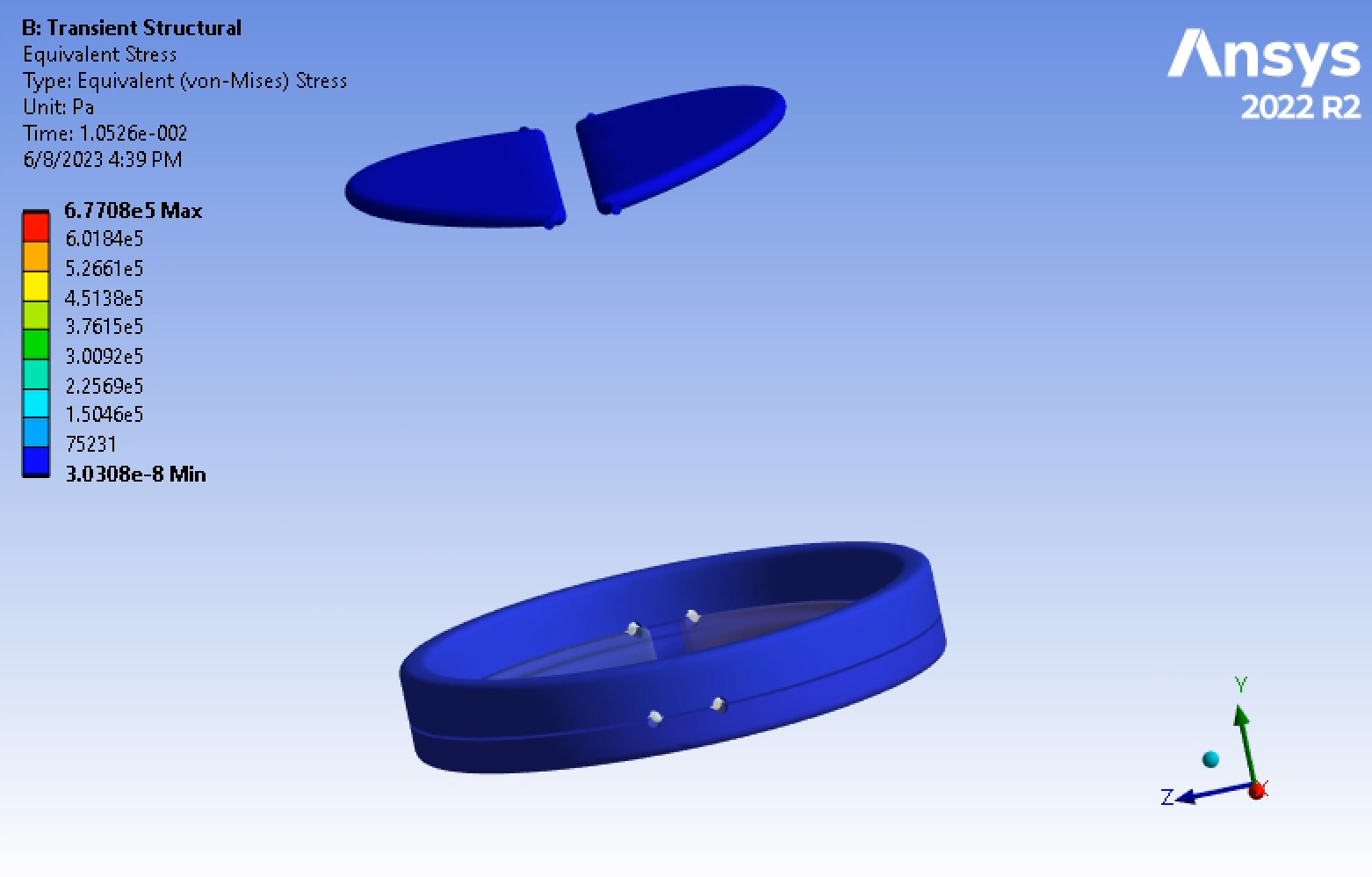
Third iteration of Transient Structural results, just two frames into the 0.2-second simulation period (representing a full ramped systolic load)
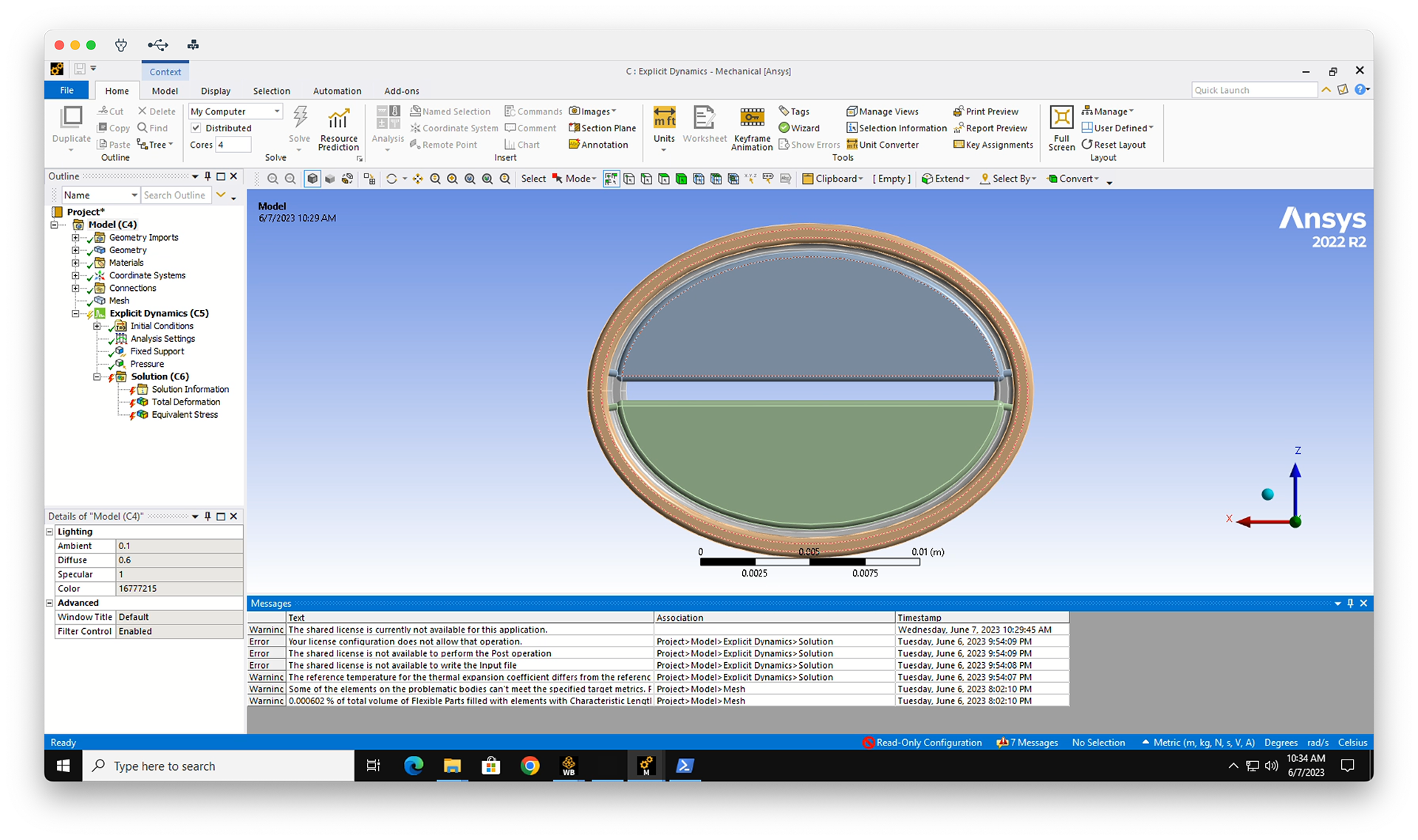
No amount of troubleshooting on my end could resolve these errors and the "Read-Only Configuration" tag on the bottom of the ANSYS window